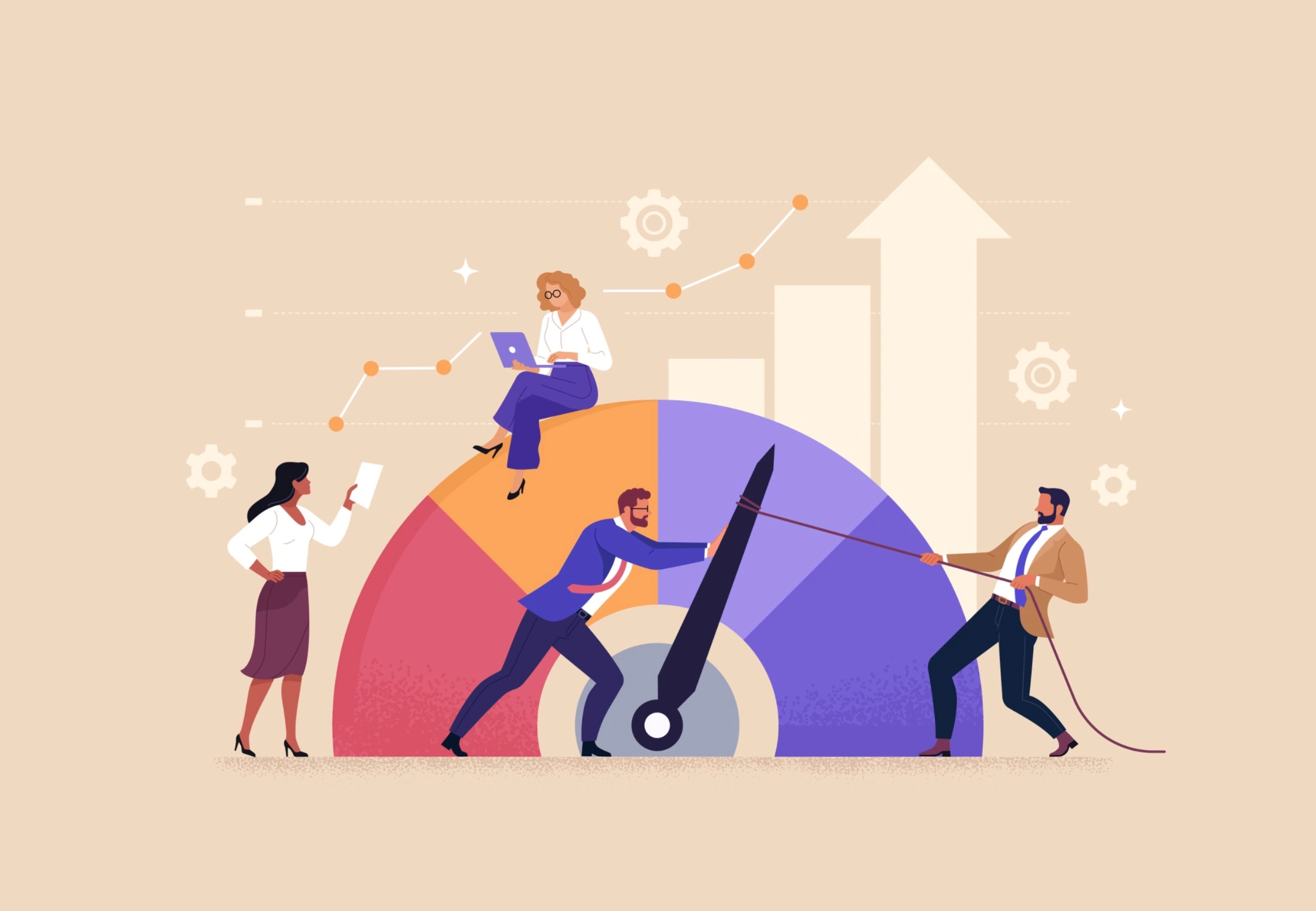
Scaling Without Breaking: Using Value Stream Mapping to Stay Efficient
Every growing company hits a point where they need to rethink their processes. Value Stream Mapping makes the process visible—and once it’s visible, it can be improved.
Early on, finding the fastest way to get something done is often the best way to get it done. And for a while, that works.
But as a business grows, the number of customers, the complexity of operations, and the dependencies between systems grow along with it. Eventually, everything starts to feel harder than it should. And when teams start searching for solutions, the problems aren’t always obvious. What used to work no longer does, and it’s not clear why.
But growth itself doesn’t break businesses—process breakdowns do. The more a company scales, the more interconnected its systems become. Every app, website, or internal tool relies on a series of processes that pass information from one step to the next. Some of these processes work smoothly. Others create unnecessary delays, duplicate work, or make users jump through hoops for no reason. A simple change in one area can have unintended ripple effects across the entire operation.
These inefficiencies are cracks that widen slowly as your business grows. Much like the proverbial lobster in a pot, you might not notice how bad things are getting until it’s critical. Luckily, we have a map for getting out of that boiling water.
What Is Value Stream Mapping?
Value Stream Mapping is a visual tool that was originally developed in the manufacturing world, most notably by Toyota, and has since become a widely used method in software development. It maps out every step of a process, helping teams optimize workflows, eliminate waste, and improve user experiences.
Value Stream Mapping shows us how work moves through a system: where it starts, how it gets processed, and where it ends up. It helps teams identify where things slow down, where extra steps are adding no real value, and where improvements can make the whole system more efficient.
Instead of treating the symptoms—adding yet another software tool, hiring more people, or building workarounds—Value Stream Mapping looks at the full picture.
How Value Stream Mapping Works
Every workflow in a business follows the same pattern:
- Something comes in (customer orders, support requests, data inputs).
- It gets processed (validated, transformed, or acted on).
- Something comes out (a fulfilled order, a resolved issue, a completed report).
In a Value Stream Map, these steps are referred to as:
- The supplier: This could be data, requests, materials, or any resource required to start an operation.
- The processor: The human, system, or workflow that takes the input from the supplier and transforms it into something of greater value.
- The customer: The recipient of the processed output, which could be an end-user, another system, or even an internal team that relies on the result.
By mapping out each of these, businesses can identify exactly where wasted effort, slowdowns, and redundancies occur, often finding them in unexpected places.
But Value Stream Mapping doesn’t just identify where problems happen—it reveals why they happen. Once businesses see the issues clearly, fixing them becomes straightforward.
The real advantage of Value Stream Mapping is that it shifts the focus from patching individual problems to fixing systemic issues. Instead of constantly reacting to breakdowns, businesses can proactively remove inefficiencies before they become major obstacles.
Value Stream Maps use a simple, structured way of visually representing how work flows through a process. They follow a common set of symbols and rules, making it easy to see where things are running smoothly and where delays or inefficiencies are happening. Information always moves from left to right, key steps are shown as boxes, and problem areas are clearly marked. Because every Value Stream Map follows the same structure, teams can quickly understand and analyze their workflows, whether they’re mapping a factory floor or a digital system.
How a Value Stream Map Is Made
A Value Stream Map is built by making a drawing of every step in a process, from start to finish, to see where work is flowing smoothly and where things are getting stuck. The process generally follows these steps:
Define the Process Scope
Specify the exact workflow being mapped. It could be a business operation, a manufacturing process, or a customer service process.
Identify Key Stakeholders
Clarify who provides inputs, who processes them, and who receives the final output. This typically includes users, developers, system components, or even automated workflows.
Map the Current State
Teams document each step in the workflow by walking through it in real-time, in person. They note who is responsible for each step, how long it takes, and what obstacles slow it down.
Analyze for Waste
Once the map is complete, inefficiencies are analyzed. Identifying waste is a huge part of the Value Stream Mapping process—one that deserves its own article—but common examples include unnecessary or redundant steps, long wait times between actions, manual tasks that could be automated, or rework caused by unclear requirements or defects.
Design the Future State
Based on the analysis, improvements are proposed to streamline the workflow, eliminate waste, and make the process more efficient. This often involves automating repetitive tasks, improving communication between teams, or reducing the number of required steps.
Implement and Measure Improvements
Once changes are made, teams track performance metrics to ensure that the new process is more efficient and that every single step provides value.
Why Value Stream Mapping Matters
Let’s look at an example of how Value Stream Mapping could improve a process. Imagine a billing department at a medical services company is falling behind on invoicing. Payments are delayed, cash flow is tight, and leadership isn’t sure where the bottleneck is. So the team creates a Value Stream Map to trace the end-to-end billing process. What they find is eye-opening:
The supplier (front office staff) collects patient details, but they're often incomplete or inconsistent. The processor (billing team) spends hours verifying insurance information and correcting errors. The customer (payment system) only accepts batches once a week, creating artificial delays.
The process isn’t broken in one place—it’s inefficient in multiple small ways that add up. With the full picture in view, they can now prioritize changes, from improving data capture at intake to automating batch submissions.
Many inefficiencies in software go unnoticed because they happen behind the scenes. Creating a Value Stream Map allows the software team to see where the hangups are and make changes to ship updates faster without sacrificing quality.
Value Stream Mapping allows teams to improve processes with clear data rather than guesswork. Instead of just treating isolated symptoms, it provides a big-picture view of how work flows, where it hits obstacles, and what it would take to clear those obstacles.
Conclusion
Process breakdowns are a natural byproduct of growth. What separates companies that are crippled by these breakdowns and those that scale past them is having leaders that respond to signs that they’ve outgrown their old ways of working. They take advantage of tools like Value Stream Mapping to analyze workflow, eliminate waste, and ensure every step adds meaningful value without unnecessary friction.
In our next article in this series, we’ll dive into all the forms waste can take, how to identify it, and how to cut it out of your business.
Share:
Link copied.
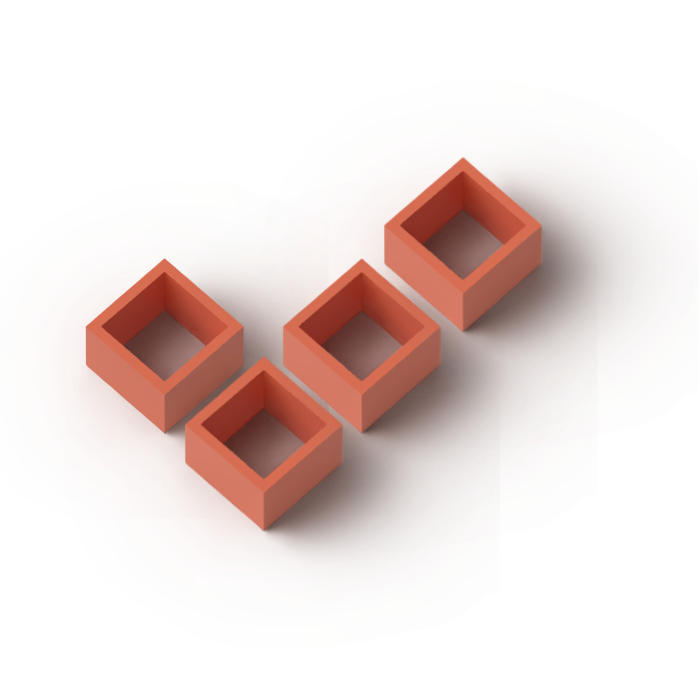
We are custom software experts that solve.
From growth-stage startups to large corporations, our talented team of experts create lasting results for even the toughest business problems by identifying root issues and strategizing practical solutions. We don’t just build—we build the optimal solution.
From growth-stage startups to large corporations, our talented team of experts create lasting results for even the toughest business problems by identifying root issues and strategizing practical solutions. We don’t just build—we build the optimal solution.